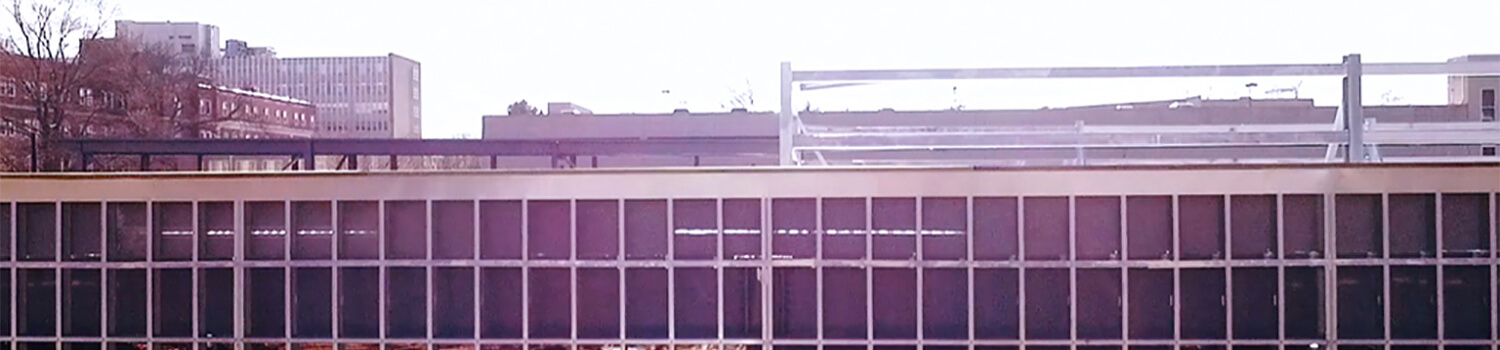
Frequently Asked Questions
It is best to bring us in early in the process to work directly with your architect and engineer. Our system can improve every phase of the CFS framing process, even if it was not designed in FRAMECAD originally. The more information about your project design that we can get up front, the faster and easier installation will be. If we are able to meet early on with electricians, plumbers and mechanical subcontractors, we can ensure that as much work as possible is done in the manufacturing and assembly stage instead of on the job site. In addition, if the project is beyond the conceptual or design phase, we would greatly appreciate you place us in the list of bidders.
The entire project. With our FRAMECAD system, you are able to design and build everything from the foundation including all load bearing and non-load bearing walls along with floor and roof trusses.
With our CFS system, every aspect of the construction process is accelerated from design through manufacturing and assembly to installation. Wall panels, joists, and trusses go up 30% - 50% faster than conventional builds. And with virtually 100% accuracy no time is wasted to errors. Also trades like MEP, carpentry work, among others, are drastically reduced not only by labor cost but also timing.
The sky is the limit. Economically, we recommend a maximum of about 4 floors, but from a design perspective CFS can go much higher. It is the perfect solution for mid-rise buildings (5 or 6 levels) that require fire rated exterior walls.
It’s easy! First, send us a set of drawings/plans for any project in CAD or .dwg format or contact our design team to start a conversation. We will review your plans to convert them with our FRAMECAD® software and provide a cost proposal.
Our FRAMECAD® software works directly from the architect's drawings so they need to be accurate.
In order to provide the best possible quote and have your project benefit from all of our product advantages, the architect should provide a full architectural set of drawings. These should include electrical, mechanical, plumbing, aside from your standard interior details.
We have two FRAMECAD® design and build machines. One machine produces 3 5/8” x 1 5/8 flange studs using 22-gauge to 18-gauge steel. The other machine produces 6” x 1 5/8 flange studs and can go down to 16-gauge steel. The gauge required for the desired project will be determined by our engineer. This is also based on the scale of the project and other factors such as cost effectiveness, pre-engineering requirements and individual building codes.
No. Any project can be built using CFS by Network Framing Solutions.
Yes, walls are designed and manufactured using the same process. If there were any restrictions in which we cannot take our pre-engineered walls pre-assembled, we will bundle them according to panel number and ship them to be assembled on-site under controlled conditions guaranteeing the same quality control we have at our facility. This is ideal for special projects because there is no need for chop-saws eliminating noise and hot work permits.
Yes. FRAMECAD® pre-engineered assemblies can be confidently used for building construction with independent certification from ICC Evaluation Service, LLC (ICC-ES). We get a lot of good feedback from building officials.
Yes. As the Northeast’s only manufacturer and installer of pre-engineered steel framing, we understand the challenges that New England winters impose on architects and engineers.
Yes, we can meet most UL Assemblies.
Using NFS pre-engineered panel design can reduce installation time by 30-50% off the framing schedule as well as the other trades essential to the construction process.
Changes are fast and easy with pre-engineered panels. They can be made on the job site with conventional methods or panels can be re-run by inputting the change into our design software to reproduce the panel in minutes for immediate delivery to the job site.
Anyone with proper training.
There are no limitations to the type of material that can go over our system.
We can install most sheathing products in our shop prior to shipping, as well as insulation and sound proof/fire barriers.
Yes, that can all be done in our facilities.
NFS can produce walls to any height to accommodate MEP trades and has developed a system to top out walls to accommodate sloped roof decks that requires little or no cutting.
Yes, we manufacture our own deflection track in our facility. We can either bundle it or install it on the panels and ship to the site.
Install time is quicker, clean and allows other trades to mobilize on site sooner. We can accommodate service holes at any height/elevation.
Seeing is Believing
Tour our facility to see how it works.